Gravity Casting
Gravity casting - is useful when dealing with aluminum and other light alloys. It can serve for parts with undercut by sand-core to meet the feature needs.
Advantages of Gravity Casting Method:
1. The mold can be repeatedly used, omit the required procedures of modeling, high production efficiency, suitable for mechanization and automation of production.
2. Mold wall surface is smooth and easy to deform the cavity, so casting a more sophisticated dimension and surface properties is
avaiable.
3. Recast using a metal mold, so faster cooling rate, fine grain structure, and no segregation, and good mechanical properties of the
casting.
4. The work environment is better than sand casting.
Feature:
Gravity casting method is competitive casting method when production quantity is relatively small or when heat treatment is needed to improve the mechanical properties. It employs cast iron or steel molds which allow aluminum and zinc castings to be produced more accurately and cheaply than with sand casting. And due to the relatively faster cooling rates that occur in gravity die casting, a better surface finish, and better mechanical properties are the advantages of gravity casting.
Materials:
■ Aluminum Alloy:A356, A319, A360, A383, A413.2, AC4C, A380, AC7A
Surface treatment: Galvanising, Cr-based and Cr-free coating, sand blasting, priming, burnishing, pickling, passivation, painting and decorative coatings and others
Product:
■ Motorcycle parts:Air-cylinder head, Outer shell of engine, Pump essence, Gear drive box, Connected-bar, Wheel.
■ Machine parts:Woodwork Machine, CNC rotary cylinder, Reduction device part, exhaust blower drum.
■ Pneumatic-oil parts:Oil pressure filters net, Front cover, Following Cover
■ Others:Shipping blade, Plastic glove model, Fire-fighting equipment.
Gravity Casting Product Size & Weight Range
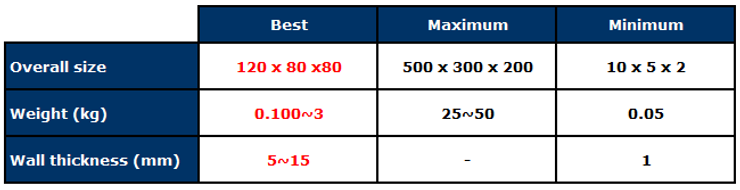
Comparison of Gravity Casting with Other Metal Fabrication Methods
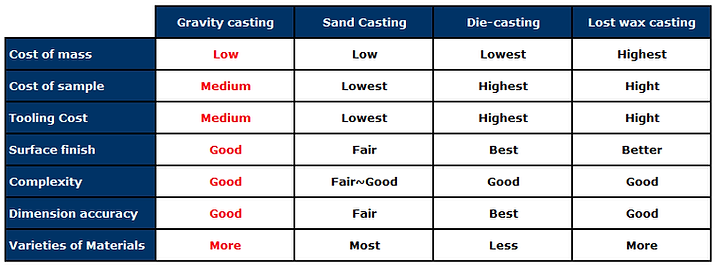
Gravity Casting Products Portfolio





